2024 / 09 / 10
640g Aluminum Alloy vs Steel N2O Cylinders: How to Choose
Table of Contents
Nitrous oxide (N2O) cylinders are crucial in various applications, including culinary uses, medical treatments, and industrial processes. Choosing the right cylinder material is essential for ensuring safety, efficiency, and cost-effectiveness. Two common materials for N2O cylinders are aluminum alloy and steel. Each material offers distinct advantages and drawbacks that influence performance, durability, and overall suitability. This article provides an in-depth comparison between 640g aluminum alloy and steel N2O cylinders to help you make an informed choice.
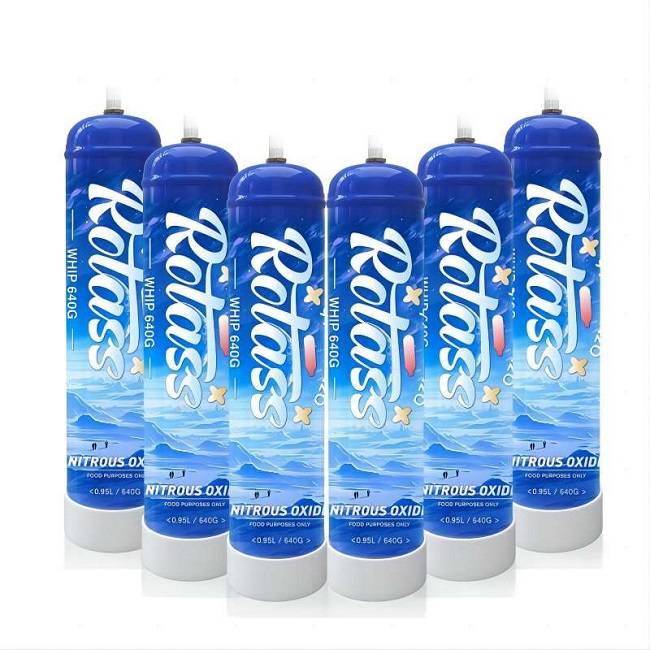
Material Composition and Properties
Aluminum Alloy 640g N2O Cylinder
Aluminum alloy N2O cylinders, particularly those weighing 640g, are popular for their lightweight nature. Aluminum alloys used in these cylinders typically include elements such as manganese, silicon, and magnesium, enhancing their strength and durability.
- Lightweight Properties: One of the most significant advantages of aluminum alloy N2O cylinders is their light weight. This characteristic makes them easier to handle, transport, and install, particularly in applications where portability is crucial, such as in culinary settings or portable medical units.
- Corrosion Resistance: Aluminum naturally forms a protective oxide layer when exposed to air, which provides excellent resistance to corrosion. This property is beneficial in preventing rust and maintaining the N2O cylinder’s integrity over time, especially in humid or moist environments.
- Thermal Conductivity: Aluminum has high thermal conductivity, which means it can dissipate heat more efficiently than steel. This property is advantageous in scenarios where the N2O cylinder might be subjected to temperature variations, as it helps in regulating the temperature of the contained gas.
Steel N2O Cylinder
Steel N2O cylinders, on the other hand, are known for their strength and durability. They are commonly made from carbon steel or alloy steel, which are known for their robustness.
- Heavier Weight: Steel cylinders are significantly heavier than their aluminum counterparts. While this can be a disadvantage in terms of portability, the added weight contributes to greater stability and robustness, making them suitable for stationary applications or environments where durability is a priority.
- Strength and Durability: Steel N2O cylinders are known for their high tensile strength and impact resistance. This makes them highly durable and able to withstand harsh conditions without deformation. They are less prone to physical damage compared to aluminum N2O cylinders.
- Susceptibility to Corrosion: Unlike aluminum, steel is more susceptible to corrosion. Without proper maintenance and protective coatings, steel N2O cylinders can rust over time, particularly in damp environments. This susceptibility requires regular inspection and maintenance to ensure safety.
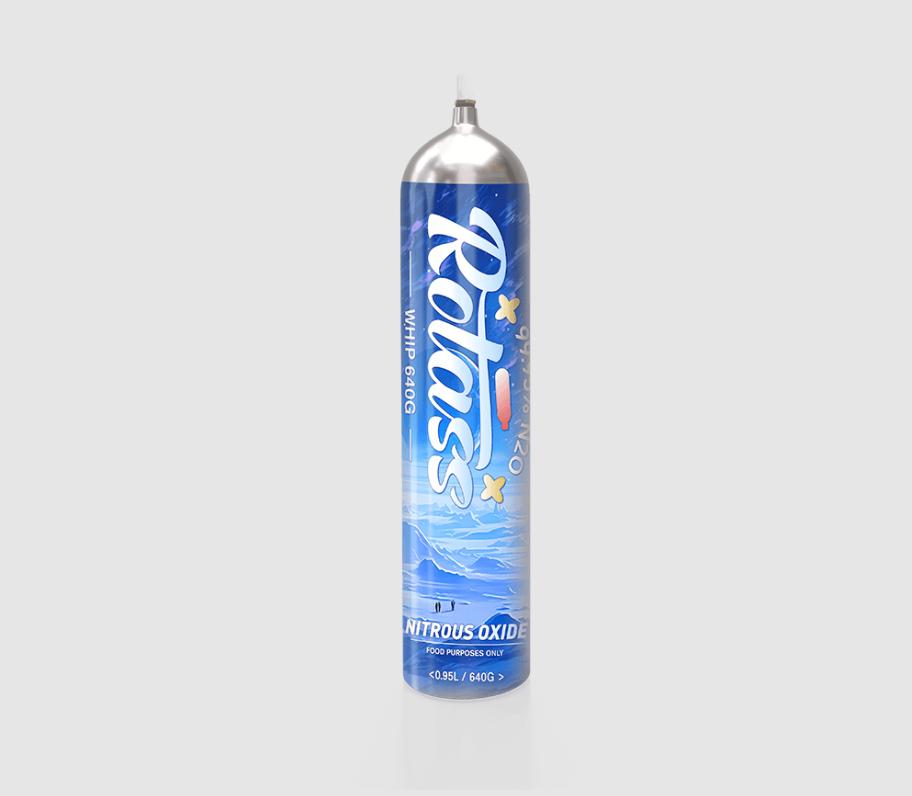
Performance and Durability
Weight Considerations
The weight of the N2O cylinder plays a critical role in its overall performance and handling.
- Aluminum Alloy: The lightweight nature of aluminum alloy N2O cylinders makes them more convenient for applications requiring frequent handling or mobility. For instance, in culinary settings where N2O cylinders are often moved and repositioned, the reduced weight of aluminum cylinders is advantageous.
- Steel: Although steel N2O cylinders are heavier, this characteristic can be beneficial in stationary applications where the cylinder’s stability is essential. The additional weight can also contribute to a lower center of gravity, reducing the risk of tipping over.
Durability
Both aluminum and steel N2O cylinders offer different types of durability.
- Aluminum Alloy: Aluminum N2O cylinders have good durability in terms of resistance to physical damage and corrosion. However, they may not be as impact-resistant as steel N2O cylinders. They are ideal for applications where exposure to environmental factors is minimal, and regular handling is a factor.
- Steel: Steel N2O cylinders are highly durable and can endure significant physical stress. They are more resistant to punctures and dents compared to aluminum. Steel N2O cylinders are suitable for high-demand applications where robustness and long-term reliability are critical.
Safety Aspects
Pressure Tolerance
The ability of a N2O cylinder to handle high pressure is crucial for safety.
- Aluminum Alloy: Aluminum N2O cylinders are designed to handle high pressures, but they typically have lower maximum pressure ratings compared to steel N2O cylinders. It is essential to ensure that the cylinder’s pressure rating aligns with the intended application to avoid potential risks.
- Steel: Steel N2O cylinders generally have higher pressure tolerance due to the material’s strength. They are often preferred in scenarios where the N2O cylinder will be subjected to high pressure or where safety margins are a primary concern.
Corrosion Resistance
Corrosion resistance is vital for maintaining the safety and longevity of the N2O cylinder.
- Aluminum Alloy: The natural corrosion resistance of aluminum makes it an excellent choice for environments where exposure to moisture or chemicals is a concern. The protective oxide layer reduces the likelihood of rust and deterioration.
- Steel: Steel N2O cylinders require protective coatings or regular maintenance to prevent corrosion. Without adequate protection, steel can rust, compromising the cylinder’s safety and integrity.
.Heat Resistance
Heat resistance is another important factor to consider.
- Aluminum Alloy: Aluminum’s high thermal conductivity helps in dissipating heat, which can be advantageous in regulating the temperature of the gas inside the cylinder. However, aluminum may have a lower tolerance to extreme temperatures compared to steel.
- Steel: Steel N2O cylinders have better heat resistance and can withstand higher temperatures without compromising structural integrity. This makes them suitable for applications involving higher thermal stress.
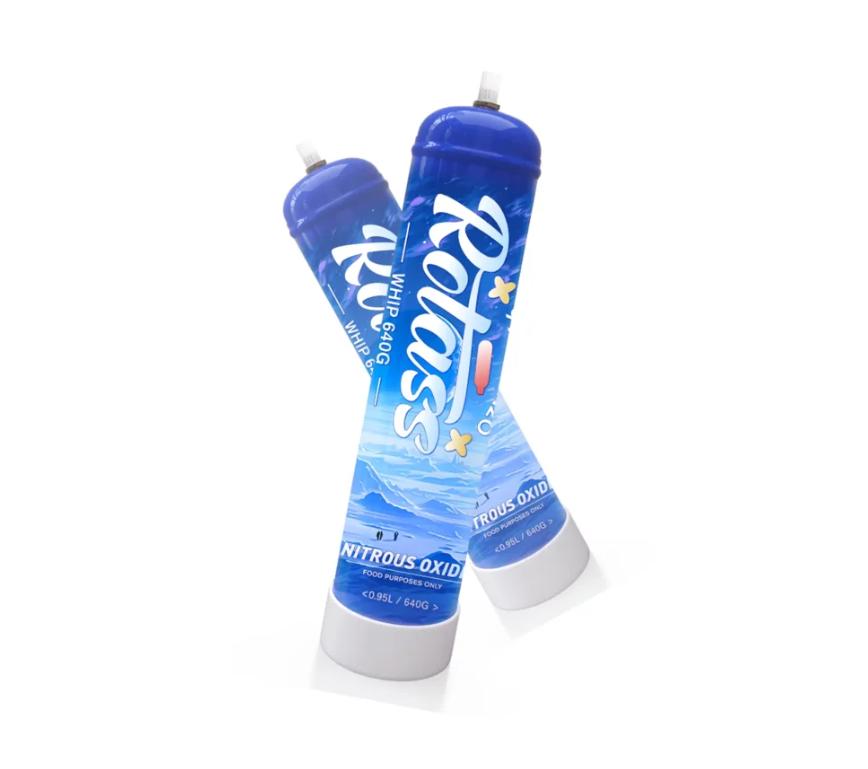
Cost-Effectiveness
Initial Purchase Price
The initial cost of the N2O cylinder can vary significantly based on the material.
- Aluminum Alloy: Generally, aluminum alloy N2O cylinders tend to be more expensive upfront due to the cost of material and manufacturing processes. However, their lightweight nature can justify the higher price in applications where mobility is crucial.
- Steel: Steel N2O cylinders are usually more cost-effective in terms of initial purchase price. They offer a lower upfront cost, making them a more economical choice for applications where budget constraints are a consideration.
Long-Term Cost Considerations
Long-term costs include maintenance, replacement, and overall lifecycle expenses.
- Aluminum Alloy: Although aluminum N2O cylinders have a higher initial cost, their corrosion resistance and lower maintenance requirements can result in reduced long-term costs. They typically have a longer lifespan in environments where corrosion is a concern.
- Steel: Steel N2O cylinders may incur higher long-term costs due to the need for regular maintenance and potential corrosion-related issues. However, their durability and strength may offset these costs in high-demand applications.
Resale Value
The resale value of the N2O cylinder can also be a factor.
- Aluminum Alloy: Aluminum N2O cylinders may have higher resale value due to their advanced properties and lower maintenance requirements. Their lightweight nature can make them appealing in secondary markets.
- Steel: Steel N2O cylinders may have lower resale value, primarily due to their susceptibility to corrosion and higher maintenance needs. However, their robustness may still be attractive to certain buyers.
Environmental Impact
Manufacturing Process
The environmental impact of manufacturing processes is a consideration for many buyers.
- Aluminum Alloy: The production of aluminum involves significant energy consumption and environmental impact, although advancements in recycling technologies are helping to mitigate these effects. Aluminum recycling is highly efficient, reducing the overall environmental footprint.
- Steel: Steel production also involves substantial energy use and environmental impact. However, steel is widely recyclable, and the recycling process helps in reducing its overall environmental impact.
Recycling and Disposal
The end-of-life disposal and recycling capabilities are important for minimizing environmental impact.
- Aluminum Alloy: Aluminum is highly recyclable, and recycled aluminum requires less energy compared to new production. The recycling process is well-established, making aluminum a more environmentally friendly option in terms of disposal.
- Steel: Steel is also highly recyclable, and the recycling process helps in reducing waste and conserving resources. The established recycling infrastructure for steel makes it a sustainable choice in terms of end-of-life disposal.
Application Scenarios
Best Use Cases for Aluminum Alloy N2O Cylinders
- Culinary Applications: Aluminum N2O cylinders are ideal for culinary uses due to their lightweight nature and corrosion resistance. They are easy to handle and transport, making them suitable for use in food preparation settings.
- Medical Uses: In medical applications where portability and ease of handling are crucial, aluminum N2O cylinders offer significant advantages. Their lightweight properties and resistance to corrosion make them suitable for mobile medical units.
Best Use Cases for Steel Cylinders
- Industrial Applications: Steel N2O cylinders are well-suited for industrial applications where durability and strength are paramount. Their ability to withstand high pressures and physical stress makes them ideal for heavy-duty use.
- Stationary Installations: For applications where the cylinder will remain stationary and stability is important, steel N2O cylinders provide the necessary robustness and durability.
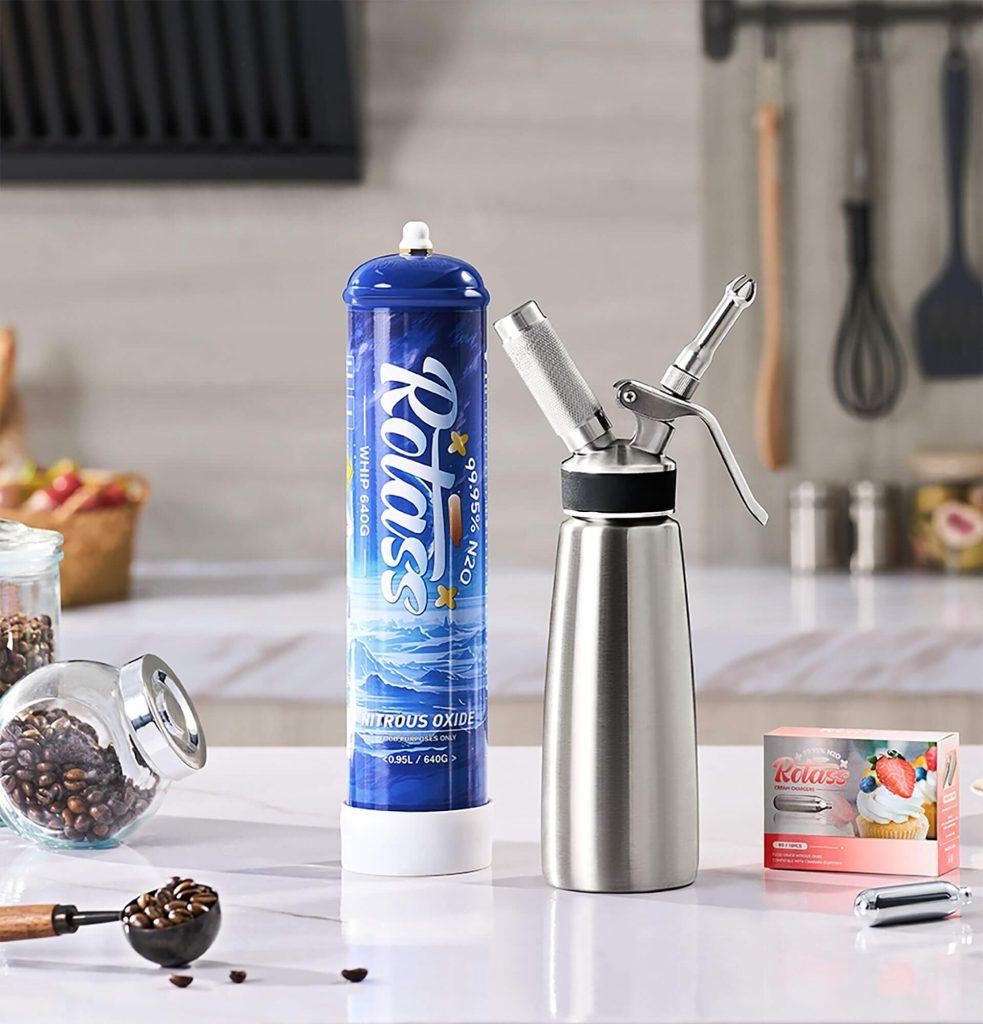
How to Choose
Choosing between a 640g aluminum alloy and a steel N2O cylinder involves evaluating various factors, including material properties, performance, safety, cost-effectiveness, and environmental impact. Aluminum cylinders offer advantages in terms of lightweight properties, corrosion resistance, and thermal conductivity, making them suitable for applications where these factors are critical. Steel cylinders, with their superior strength, durability, and lower initial cost, are ideal for high-pressure applications and scenarios where weight is less of a concern.
Ultimately, the choice between aluminum alloy and steel N2O cylinders should be based on the specific requirements of the application, budget considerations, and environmental impact. By carefully assessing these factors, you can make an informed decision that ensures safety, performance, and cost-effectiveness for your needs.